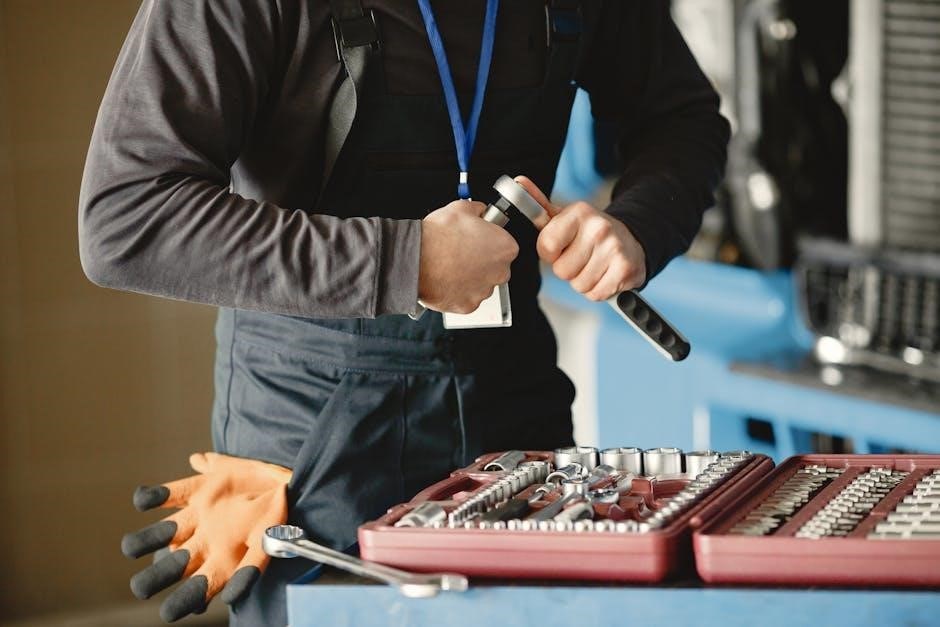
A torque wrench is a precision instrument used to apply a specific torque to screws, bolts, and nuts, ensuring proper tightening without over-tightening. It’s essential for mechanical and industrial applications to maintain safety and consistency in fastening processes.
1.1 What is a Torque Wrench?
A torque wrench is a precision tool designed to apply a specific amount of rotational force, measured in foot-pounds (ft-lb) or Newton-meters (Nm), to screws, bolts, or nuts. It ensures proper tightening without over-tightening, which can damage materials or compromise structural integrity. commonly used in automotive, mechanical, and industrial settings, torque wrenches are essential for maintaining safety and consistency in fastening processes. They feature adjustable torque settings, allowing users to preset the desired force, and often provide an audible signal or tactile feedback when the target torque is reached. This ensures accurate and reliable application of force, making them indispensable for precise mechanical tasks.
1.2 Importance of Using a Torque Wrench
Using a torque wrench is crucial for ensuring the integrity of mechanical components by preventing over-tightening, which can lead to material damage or fastener failure. Proper torque application guarantees that parts are securely fastened without excessive stress, enhancing safety and durability. In industrial and automotive applications, precise torque control minimizes the risk of equipment malfunction and extends the lifespan of machinery. Additionally, it reduces the likelihood of costly repairs by avoiding stripped threads or damaged bolts. Using a torque wrench also promotes consistency across multiple fasteners, ensuring uniform stress distribution and reliability in critical joints. This makes it an essential tool for professionals and DIYers alike, providing peace of mind and professional-grade results.
1.3 Brief History and Evolution
The concept of torque wrenches dates back to the early 20th century, evolving from basic mechanical tools to precise instruments. Initially, torque wrenches were simple devices with limited adjustability, primarily used in industrial settings. Over time, advancements in materials and engineering led to the development of adjustable torque wrenches, allowing users to set specific torque values. The introduction of digital torque wrenches in the late 20th century revolutionized the field, offering greater accuracy and ease of use. Modern torque wrenches combine ergonomic design, advanced materials, and digital technology to provide unparalleled precision and reliability. This evolution reflects the growing demand for consistency and safety in mechanical applications across industries.
Safety Guidelines
Always wear safety gear and follow proper handling techniques. Ensure the wrench is used correctly to avoid injury or damage, adhering to all safety protocols meticulously.
2.1 General Safety Precautions
Always follow safety guidelines when using a torque wrench to prevent accidents. Wear protective gear, including gloves and safety glasses, to minimize risks. Ensure the wrench is properly calibrated and adjusted before use. Avoid using the wrench as a breaker bar or pry bar, as this can cause damage or injury. Keep hands and body parts away from moving components. Secure the socket firmly to the drive to prevent slippage. Never exceed the recommended torque range for the wrench or fastener. Regularly inspect the tool for wear or damage, and replace worn parts immediately. Use the wrench only for its intended purpose, and avoid applying excessive force; Store the tool in a dry, secure location when not in use. Always refer to the manual for specific safety recommendations.
2.2 Proper Handling Techniques
Hold the torque wrench with a firm, balanced grip, keeping your hands centered on the handle to maintain control. Apply force slowly and steadily, avoiding sudden movements. Ensure the socket is securely attached to the square drive to prevent slippage or tilting. Keep the wrench perpendicular to the bolt or nut to maintain even force distribution. Avoid using the wrench as a breaker bar or hammer, as this can damage the tool or fastener. After tightening, release the force gradually to avoid sudden stops. Always return the wrench to its lowest torque setting when not in use to prevent internal stress. Regularly inspect the handle and head for wear or damage, and ensure all moving parts are well-lubricated for smooth operation.
2.3 Safety Clothing and Equipment
When using a torque wrench, wear appropriate safety gear to minimize risks. Safety glasses or goggles protect against flying debris, while gloves provide grip and prevent hand injuries. A face mask is recommended in dusty environments. Steel-toe boots and long sleeves can safeguard against accidental tool slippage. Ensure loose clothing or jewelry is secured to avoid entanglement. Keep the workspace well-lit to maintain clear visibility. Avoid wearing jewelry that could get caught in moving parts. Use a torque wrench with a secure socket attachment to prevent it from slipping off and causing injury. Regularly inspect safety equipment for wear and replace as needed to ensure optimal protection during operation.
Components of a Torque Wrench
A torque wrench consists of a handle, drive head, adjustable mechanism, and scale. The handle provides grip, the drive head connects to sockets, and the mechanism adjusts torque settings. Digital models include an LCD screen for precise readings. Understanding these components is crucial for proper operation and maintenance.
3.1 Exploded View of a Torque Wrench
An exploded view of a torque wrench reveals its internal components, including the handle, drive head, adjustable mechanism, and torque scale. The handle provides grip and leverage, while the drive head connects to sockets. The adjustable mechanism allows setting precise torque values, and the torque scale displays these settings. Digital models may include an LCD screen and electronic controls. The ratchet assembly enables smooth operation, and internal gears transmit force to the bolt or nut. Understanding this view helps in assembling, maintaining, and troubleshooting the wrench. Regular maintenance of these components ensures accuracy and longevity. Always refer to the manual for specific assembly details and safety precautions to avoid damage or improper use. Proper care extends the tool’s lifespan and reliability in various applications.
3.2 Main Parts and Their Functions
The torque wrench comprises several key components, each serving a specific function. The handle provides a comfortable grip and leverage for applying force. The drive head, often a square or hexagonal socket, connects to various attachments. The adjustable mechanism allows users to set the desired torque, typically via a rotating dial or micrometer. The torque scale displays the set value, ensuring precision. Digital models feature an LCD screen for easy reading. The ratchet assembly facilitates smooth, efficient operation, while internal gears transmit the applied force. The locking mechanism secures the torque setting, preventing accidental adjustments. Together, these parts ensure accurate and consistent torque application, critical for preventing damage to bolts and ensuring safety in industrial and mechanical tasks.
3.3 Types of Torque Wrenches (Adjustable, Digital, etc.)
Torque wrenches are available in various types to suit different applications. Adjustable torque wrenches allow users to set the desired torque value manually, offering flexibility across multiple tasks. Digital torque wrenches feature electronic displays and precise torque control, often with preset modes and memory functions for repeated use. Fixed torque wrenches are pre-set to a specific torque value, ideal for applications requiring consistent tightening. Hydraulic and pneumatic torque wrenches are used in heavy-duty industries for high-torque applications. Cordless torque wrenches offer portability and ease of use, while breakout wrenches are designed for loosening bolts before applying precise torque. Each type is tailored to specific needs, ensuring efficient and accurate torque application in diverse settings.
Choosing the Right Torque Wrench
Selecting the correct torque wrench involves considering torque range, drive size, and application. Adjustable wrenches offer flexibility, while digital models provide precision. Match the wrench to the task for optimal performance and safety.
4.1 Understanding Torque Measurements (ft-lb, Nm)
Torque measurements are crucial for accurate tightening. Torque is typically expressed in foot-pounds (ft-lb) or Newton-meters (Nm). Understanding these units ensures proper use of the wrench. The user must convert units if necessary, using conversion factors like 1 Nm = approximately 0.7376 ft-lb. Always refer to the manual for specific torque values. Proper measurement prevents over-tightening, which can damage components, and under-tightening, which may lead to loosening over time. Using the correct torque ensures safety and reliability in mechanical applications. Always verify the torque setting before applying force to avoid errors. This step is essential for maintaining precision and avoiding potential hazards. Proper torque measurement is fundamental for effective and safe tool usage.
4.2 Selecting the Correct Drive Size
Selecting the correct drive size is essential for proper torque wrench operation. Common drive sizes include 1/4″, 3/8″, 1/2″, and 3/4″. The drive size must match the socket being used to ensure a secure fit. Using an incorrect drive size can lead to slippage, which may result in inaccurate torque application or damage to the wrench. Always verify the drive size compatibility with the socket and the fastener being tightened. Proper alignment and fit prevent wear on the wrench and ensure precise torque delivery. Refer to the instruction manual for drive size recommendations specific to your torque wrench model. Correct drive size selection is critical for safe and effective tool usage.
4.3 Torque Range and Application
Choosing the correct torque range ensures accurate and safe application. Always match the wrench’s torque range to the task’s requirements. Exceeding the maximum torque can damage the tool or the fastener. For applications requiring precise control, digital torque wrenches offer preset torque values, emitting a clear signal upon reaching the set torque. Adjustable wrenches allow flexibility across various tasks, while fixed wrenches are ideal for repetitive operations. Proper torque application prevents over-tightening, which can strip threads or damage materials. Ensure the wrench is calibrated and maintained regularly for consistent performance. Correct torque range selection is vital for achieving professional results and protecting both the tool and the workpiece. Always refer to the instruction manual for specific torque recommendations tailored to your wrench model and application.
Operating Instructions
Attach the correct socket to the wrench, set the desired torque, and apply steady force until the audible click confirms the torque is reached. Always follow manual guidelines.
5.1 Setting the Torque Value
To set the torque value, start by loosening the locking screw or collar on the wrench. Rotate the adjustable grip until the desired torque aligns with the marker. Use a hex key for precise adjustments, turning clockwise to increase torque and counterclockwise to decrease it. Once set, tighten the locking mechanism to secure the torque value. Always approach the target torque from a lower setting to avoid overshooting. For digital models, use the keypad to input the exact value and confirm with the “Set” button. Ensure the wrench is calibrated and stored properly when not in use to maintain accuracy. Refer to the manual for specific instructions tailored to your wrench model.
5.2 Using the Torque Wrench
Attach the appropriate socket to the wrench’s square drive, ensuring it fits securely. Position the socket on the fastener, aligning it properly to avoid tilting. Grasp the handle firmly and apply steady, controlled force. As torque is applied, listen for the audible “click” or feel the slight impulse, indicating the set torque has been reached. Stop immediately upon hearing the click to prevent over-tightening. For low torque settings, the click may be subtle, so use the wrench in a quiet environment. Always maintain control of the wrench to ensure accurate and safe operation. Do not use the wrench as a breaker bar or apply excessive force beyond the set torque. Proper technique ensures precision and prevents damage to components.
5.3 Understanding the Audible Signal (Click)
The audible signal, or “click,” is a mechanism that alerts the user when the desired torque has been reached. This feature ensures precise control and prevents over-tightening. When the set torque is applied, the wrench releases a distinct clicking sound accompanied by a slight impulse in the handle. The click indicates that the target torque has been achieved, and further force should not be applied. At low torque settings, the click may be less pronounced, so it’s important to use the wrench in a quiet environment. The signal is both auditory and tactile, providing a clear indication to stop tightening. This mechanism enhances accuracy and safety, making it essential to rely on the click rather than guessing when the torque is met.
Maintenance and Care
Regular maintenance ensures optimal performance and longevity of your torque wrench. Store it in a dry place, avoiding extreme temperatures. Always return the adjustment to its lowest setting when not in use. Clean the tool with light oil after each use and lubricate moving parts periodically. Avoid exposing it to harsh chemicals or abrasive materials. Handle with care to prevent damage to internal mechanisms. Refer to the manual for specific calibration requirements to maintain accuracy over time.
6.1 Storage Recommendations
Proper storage is crucial for maintaining the accuracy and longevity of your torque wrench. Always store it in a clean, dry place away from extreme temperatures and humidity. Avoid exposing the tool to direct sunlight or moisture, as this can damage the internal mechanisms. When not in use, return the torque wrench to its lowest setting to relieve tension on the internal spring. Store the wrench in a protective case or pouch to prevent scratches and damage. Avoid storing it in environments with harsh chemicals or abrasive materials. Regularly inspect the storage area to ensure it remains free from dust and debris. Proper storage practices will help maintain the tool’s calibration and ensure reliable performance for future use.
6.2 Calibration Requirements
Calibration is essential to ensure the accuracy and reliability of your torque wrench. Regular calibration prevents measurement errors and maintains the tool’s precision. It is recommended to calibrate the wrench before its first use and periodically thereafter, ideally every six months or after a significant drop. Use a certified torque tester or calibration service to verify the wrench’s accuracy. Always follow the manufacturer’s calibration instructions or refer to a professional if unsure. Proper calibration ensures the wrench delivers the correct torque, preventing over-tightening or under-tightening of fasteners; Never use a torque wrench that has not been calibrated, as this can lead to equipment damage or safety hazards. Calibration is a critical step in maintaining the tool’s performance and reliability over time.
6.3 Cleaning and Lubrication
Regular cleaning and lubrication are crucial for maintaining the performance and longevity of a torque wrench. Use a soft cloth to wipe down the tool, removing dirt, grease, or debris that may interfere with its operation. For more thorough cleaning, a mild solvent can be applied, but avoid harsh chemicals that might damage the finish. After cleaning, apply a light oil to moving parts, such as the ratchet assembly and pivot points, to ensure smooth operation; Lubrication helps prevent corrosion and wear, keeping the wrench accurate and reliable. It is important to follow the manufacturer’s recommendations for the type of lubricant and frequency of application. Proper care ensures the torque wrench remains in optimal condition for precise torque measurements and consistent performance over time. Regular maintenance is key to extending the tool’s lifespan and ensuring accuracy in every use.
Troubleshooting Common Issues
Troubleshoot common torque wrench issues by identifying symptoms like slipping, lack of click, or adjustment failure. Regular calibration, lubrication, and proper storage can prevent these problems.
7.1 Torque Wrench Not Holding Adjustment
If the torque wrench fails to hold its adjustment, inspect for worn or damaged internal components. Ensure the locking mechanism is securely tightened and not loose. Clean and lubricate moving parts to maintain smooth operation. Avoid over-tightening, as this can strain internal gears. If the issue persists, recalibrate the wrench according to the manufacturer’s instructions or seek professional calibration. Regular maintenance, such as storing the wrench at its lowest torque setting, can prevent this problem. Never use the wrench as a breaker bar, as this can damage internal mechanisms. Proper handling and storage are crucial to ensure consistent performance and accuracy over time.
7.2 Wrench Slip or Lack of Click
If the torque wrench slips or fails to produce the audible click, check the socket connection to ensure it’s securely attached. A loose socket can cause slippage and inconsistent torque application. Inspect the drive head for wear or damage, as this can affect the wrench’s ability to engage properly. Lubricate the ratchet mechanism if it feels stiff or sticking. If the click mechanism is not functioning, it may indicate internal wear or misalignment. In such cases, recalibrate the wrench or replace worn components. Always operate the wrench in a quiet environment to easily detect the click, especially at lower torque settings. Proper maintenance and regular inspection are essential to prevent these issues and ensure accurate torque delivery.
7.3 Damage and Repair
Detecting damage early is crucial for maintaining the accuracy and functionality of a torque wrench. Inspect for signs of wear, such as scratches on the shaft, damaged sockets, or a loose handle. If the wrench is dropped or subjected to excessive force, immediately check its calibration. For minor issues, like a worn ratchet, replace the component according to the manufacturer’s instructions. For major damage, such as a bent shaft, seek professional repair or replace the tool. Never attempt to repair internal mechanisms without proper expertise, as this can lead to further damage. Regular maintenance and careful handling are essential to extend the lifespan of the torque wrench and ensure reliable performance. Always refer to the user manual for specific repair guidelines.
Advanced Topics
Explore advanced techniques for using torque wrenches, including digital models, adjustable mechanics, and compatibility with impact sockets. Discover how these tools enhance precision and efficiency in complex tasks.
8.1 Using a Digital Torque Wrench
A digital torque wrench offers precise control and real-time feedback, making it ideal for critical applications. To use it, power on the wrench and set the desired torque using the digital display. Many models allow switching between units like ft-lb and Nm. Once set, attach the appropriate socket and apply steady force until the wrench signals the target torque with a click or buzzer. Some digital wrenches store multiple torque values for quick access. Always calibrate the tool before first use and after significant adjustments for accuracy. Regular maintenance, such as cleaning and lubricating internal parts, ensures optimal performance. Digital torque wrenches are highly versatile and are preferred in professional settings for their precision and ease of use.
8.2 Adjustable Torque Wrench Mechanics
An adjustable torque wrench employs a micrometer mechanism to set specific torque values. By rotating the handle, users can adjust the internal spring tension, which determines the torque limit. The wrench signals when the set torque is reached through an audible click or tactile feedback. Adjustments are made by turning the micrometer scale clockwise to increase torque or counterclockwise to decrease it. Precision engineering ensures consistent and accurate torque application. Regular calibration is essential to maintain accuracy, and storing the wrench at its lowest torque setting preserves the internal mechanism. Proper maintenance, including lubrication of moving parts, extends the tool’s lifespan and ensures reliable performance across various applications. This design makes adjustable torque wrenches versatile for both professional and DIY use.
8.3 Torque Wrench and Impact Sockets
A torque wrench is often paired with impact sockets for high-torque applications. These sockets are designed to withstand the intense forces generated by impact wrenches and pneumatic tools. Unlike standard sockets, impact sockets are forged with tougher materials and deeper wells to prevent rounding of bolts. The combination of a torque wrench and impact socket ensures precise control over the fastening process, reducing the risk of over-tightening or stripping. Proper alignment is crucial, as misalignment can lead to uneven torque distribution and potential damage to the socket or wrench; Always ensure the socket is securely attached to the torque wrench’s square drive to maximize efficiency and safety during operation. This pairing is ideal for heavy-duty tasks in automotive and industrial settings.
A torque wrench is a valuable tool for precise fastening. Always use it correctly, follow safety guidelines, and maintain it regularly for optimal performance and longevity.
9.1 Summary of Key Points
A torque wrench is a precision tool designed to apply a specific torque to screws, bolts, and nuts, ensuring proper tightening without over-tightening. Proper usage involves setting the desired torque, attaching the correct socket, and applying force steadily until the audible signal is heard. Regular maintenance, such as calibration, cleaning, and lubrication, is essential for accuracy and longevity. Always store the wrench at its lowest torque setting and avoid using it as a breaker or pry bar. Safety guidelines, including wearing protective gear and following manufacturer instructions, must be adhered to. Digital wrenches require additional care, such as periodic recalibration, to maintain precision. Proper handling and storage ensure reliable performance and extend the tool’s lifespan.
9.2 Final Tips for Effective Use
Always follow the instruction manual for specific torque wrench models, as features may vary. Ensure the wrench is calibrated regularly for accuracy and store it at the lowest torque setting when not in use. Use the correct socket size to avoid slipping and apply force steadily, listening for the audible click. Avoid using the wrench as a breaker or pry bar, as this can damage internal mechanisms. Clean and lubricate moving parts periodically to maintain smooth operation. For digital models, refer to the manual for battery care and software updates. By adhering to these tips, you can ensure safe, precise, and long-lasting use of your torque wrench in various applications.